Plachete de siliciu: dificil defabricat și cu bariere ridicate. Acest articol descrie procesul de fabricare aplachetelor, analiza costurilor de fabricație și principalele bariere.
Procesul de fabricare aplachetelor
Materia primă pentruplachetele de siliciu este cuarțul, denumit în mod obișnuit nisip, care poate fi extras direct din natură.Procesul de fabricare a plachetelor poate fi realizat în mai multe etape.Dezoxidare și purificare, rafinare a polisiliciului, lingouri monocristaline (tije),tumbling, tăierea plachetelor, lustruirea plachetelor, recoacere,testare, ambalare și alte etape.
Dezoxidare și purificare: Materia primă pentruinstalațiile de fabricare a plachetelor de siliciu este minereul de cuarț, principala materie primă pentruminereul de cuarț fiind dioxidul de siliciu (SiO2). Minereul de cuarț este mai întâi dezoxigenat și purificat într-un proces care include sortarea,separarea magnetică, flotația, degazarea la temperaturi ridicate și așa mai departe. Principalele impurități din minereu sunt îndepărtate, cum ar fi fierul,aluminiul și alte impurități.
Rafinarea siliciuluipolicristalin: După obținerea SiO2 relativ pur, se realizează o reacție chimică pentru a produce siliciu monocristalin. Reacția principală este SiO2 + CàSi + CO, cu monoxid de carbon (CO) ca gaz, care se evaporă directdupă încheierea reacției. Astfel, rămân doar cristalele de siliciu. În acest moment,siliciul este policristalin și grosier, cu unele impurități, cum ar fi fier, aluminiu, carbon, bor, fosfor,cupru și așa mai departe. Pentru a filtra excesul de impurități, siliciul brut rezultat trebuie să fie spălat cuacid, folosind în mod obișnuit acid clorhidric (HCl), acid sulfuric (H2SO4) etc.Conținutul de siliciu după imersiunea în acid este, în general, de peste 99,7%.În timpul procesului de decapare, fierul, aluminiul și alte elemente sunt dizolvate în acid și filtrate. Cu toate acestea, siliciul reacționează, de asemenea, cu acidul pentru a forma SiHCl3(triclorură de siliciu) sau SiCl4 (tetraclorură desiliciu). Cu toate acestea, ambele substanțe sunt gazoase, astfel încât, după spălareacu acid, impuritățile inițiale, cum ar fi fierul și aluminiul, au fost dizolvate în acid, dar siliciul atrecut în stare gazoasă. În cele din urmă, SiHCl3 sau SiCl4 gazos de înaltăpuritate este redus cu hidrogen pentru a obține polisiliciu de înaltă puritate, SiHCl3+H2àSi+3HCl, SICl4+2H2àSi+4HCl. înacest punct se obține polisiliciu pentru producție.
CZ (metoda de tragere directă)
Metoda tragerii drepte (CZ) aplachetelor de siliciu este utilizată în principal în cazul cipurilor logice și de memorie și reprezintă aproximativ 95% din piață; metoda tragerii drepte a luat naștere în 1918, când Czochralski a tras filamente finedin metal topit, de unde și numele de metoda CZ. Aceasta este tehnologiadominantă pentru cultivarea siliciului monocristalin înprezent. Principalul proces implică plasarea polisiliciului într-un creuzet, încălzireaacestuia până la topire, apoi prinderea unei bucăți de cristal de sămânță de siliciu monocristal, suspendarea acesteia deasupracreuzetului și tragerea ei în linie dreaptă, cu un capăt introdus în topitură până latopire, apoi rotirea lentă și ridicarea ei în sus. În acest fel, la interfața dintre lichid și solid se formează un singur cristal prin condensare treptată.Deoarece întregul proces poate fi considerat ca o replicare a cristalelor de sămânță, cristalele de siliciu rezultate sunt cristale unicede siliciu. În plus, dopajul plachetelor se realizează, deasemenea, în timpul procesului de extracție a monocristalelor, de obicei atât în fază lichidă, cât și în fază gazoasă. Dopajul în fază lichidă înseamnă că creuzetul este dopat cu elemente de tip P sau N, carepot fi trase direct în tija de siliciu în timpul procesului de tragere amonocristalelor.
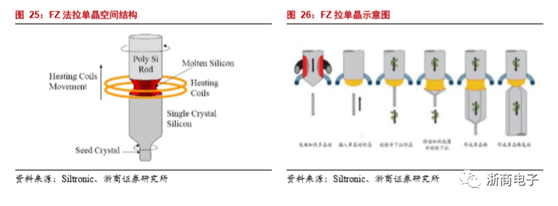
Rularea diametrului: Deoareceeste dificil de controlat diametrul tijelor de siliciu monocristal în timpulprocesului de tragere a monocristalelor, pentru a obține diametre standard, cum ar fi 6", 8", 12"etc., tijele de siliciu sunt rulate și șlefuite. După ce se extrage un singur cristal, diametrul lingouluieste laminat și rectificat, rezultând o suprafață netedă și o eroare dimensională mai mică.
Tăiere și șanfrenare: După obținerea lingourilor, se taie plachetele. Lingourilesunt plasate pe un tăietor staționar și se taie în conformitate cu programul de tăierestabilit. Datorită grosimii mici a plachetelor de siliciu, marginileplachetelor tăiate sunt foarte ascuțite. Scopul șanfrenării este de a crea o margine netedă.Placheta șanfrenată are o tensiune centrală mai mică, ceeace o face mai rezistentă și mai puțin predispusă la fragmentare la fabricarea ulterioară acipurilor.
Lustruire: Scopul principal allustruirii este de a face suprafața plăcuței mai netedă, plană și fără deteriorări și de a asigura o grosime constantă de lao plăcuță la alta.
Testarea și ambalarea: După obținerea plachetelor lustruite, este necesar să setesteze proprietățile electrice ale acestora, cum ar fi rezistivitatea și alți parametri. Cele mai multe fabrici de discuri au unserviciu de discuri epitaxiale, iar dacă sunt necesare discuri epitaxiale, atunci se realizează creșterea epitaxială a discurilor. În cazul în care nu este nevoie deplachete epi, acestea sunt ambalate și expediate către alte fabrici de plachete epitaxiale sau fabrici deplachete.
FZ (zonare fracționată)
Plachetele de siliciu cu fuziunede zonă (FZ) sunt utilizate în principal în unele cipuri de putere, cu o cotă de piață de aproximativ 4%; plachetele de siliciu realizate cuFZ (fuziune de zonă) sunt utilizate în principal pentru dispozitive deputere. Dimensiunile plăcilor sunt în principal de 8" și 6", iar în prezent, aproximativ 15% dintre elesunt realizate prin metoda FZ. În comparație cu plachetele realizate prin metoda CZ, metoda FZse caracterizează printr-o rezistivitate relativ ridicată, opuritate mai mare și o rezistență la tensiuni înalte, dar este mai dificil de realizat plachete de maridimensiuni și are proprietăți mecanice slabe, astfel încât este adesea utilizată pentruplachete pentru dispozitive de putere și mai rar pentru circuite integrate.
Metoda de fuziune zonală pentrufabricarea tijelor de siliciu monocristalin constă în trei etape: încălzireapolisiliciului, contactul cu cristalul de sămânță și tragerea monocristalului prin rotirea acestuia înjos. Într-o cameră de cuptor sub vid sau gaz inert, se utilizează uncâmp electric pentru a încălzi tijele de polisiliciu până cândpolisiliciul din zona încălzită se topește, formând o zonă topită. Zona topită este apoi atinsă cu cristale de semințe și topită. În cele din urmă, zona topită de pe polisiliciu este mutatăcontinuu în sus prin deplasarea poziției de încălzire a câmpului electric, în timp ce cristalele de sămânță se rotesc încet și se întind în jos, formând treptat tije de siliciumonocristal. Deoarece nu se utilizează creuzete în metoda de topire în zonă, seevită multe surse de contaminare, iar monocristalele extrase prin metoda detopire în zonă se caracterizează prin puritatea lor ridicată.
Analiza costurilor de producție a plachetelor
Costuri de producție a plăcilor de energie nouă
Costul plachetelor fotovoltaicepoate fi împărțit, în linii mari, în costul siliciului, costulcristalelor lungi și costul tăierii. Costul siliciului este principala parte careconsumă costuri, reprezentând aproximativ 50% din costul total. Principala diferență de cost între plachetele monocristaline și cele policristaline se află înprocesul de cristalizare lungă, deoarece siliciul monocristalin și cel policristalin au cerințe diferite pentru procesul de cristalizare lungă. Înprocesul de tăiere, producătorii de wafere pot crește cantitatea de wafere tăiatepentru a împărți costurile. Costurile cu echipamentele, energiaelectrică, gazele speciale și costurile cu forța de muncă în procesul de obținere a cristalului lung etc.
Costurile de producție monocristalină: În ceea ce privește costurile de fabricare a siliciului și de tranșare, diferența dintre siliciul monocristalin și cel policristalin nu este semnificativă.Segmentul cu cristale lungi reprezintă principala diferență de cost. În ceea ce privește structura de cost a plachetelor de siliciumonocristalin, costul materialului de siliciu reprezintăaproximativ 50%, costul de tragere a tijelor de siliciu monocristalin reprezintăaproximativ 33% din costul total, iar costul de tăiere reprezintăaproximativ 17%. Costul creuzetului și energia electrică sunt principalele surse de cost în structuracosturilor procesului de extracție monocristalină, ambele reprezentând un total de aproximativ 45%.Costurile rămase sunt dominate de câmpul fierbinte de grafit și de costurile de depreciere. În ceea ce privește costurile creuzetului, creuzetul de cuarț utilizat pentru extragerea monocristalelor se poatefisura sau rupe după temperaturi ridicate, răcire etc., ceea ce îl faceinutilizabil din nou. De asemenea, deoarece curățenia creuzetului este foarte mare pentru tragerea monocristalelor, curățenia creuzetului utilizat nu poate fi garantată, iarcalitatea creuzetului este ridicată pentru siliciul monocristalin. Prin urmare,creuzetele pentru extracția monocristalelor sunt mai scumpe și nu pot fi refolosite. În ceea ce privește costurile energiei electrice, producătoriiinterni de plachete semiconductoare sau producătorii de plachete fotovoltaiceconstruiesc fabrici în Mongolia interioară, Yunnan, Guizhou și în alte regiuni unde costurile energiei electricesunt relativ scăzute, ceea ce contribuie la reducerea costurilor.Reducerea costului plachetelor de siliciu monocristalin provine din trei surseprincipale. În primul rând, creșterea producției de cuptoare unice a dus la reducereaconsumabilelor de unică folosință, cum ar fi creuzetele și amortizarea echipamentelor. În al doilea rând,costurile mai mici ale energiei electrice. În al treilea rând, avantajul de preț al achiziției în vrac de siliciu.
Costurile de fabricație a polisiliciului: Procesul de fabricație a polisiliciului nu necesităextragerea de cristale unice, astfel încât costul cristalelor lungi este relativscăzut. Costul cristalelor lungi reprezintă doar 12% din costul total. Principala sursă decost este costul siliciului, care reprezintă aproximativ 52% din costul total. Aceasta este urmată dereducerea costurilor, care reprezintă aproximativ 29% din costurile totale. Domeniulfierbinte al grafitului reprezintă cea mai mare parte a costurilor cristalelor lungi depolisiliciu, cu 28%. Acestea sunt urmate de costurile cu creuzetul, amortizareași energia electrică, cu 16,7%, 16,7% și, respectiv, 13,9%. Deoarece plachetele de siliciupolicristalin sunt utilizate în principal în produsele fotovoltaice și au tendința de a fi înlocuite treptat cu plachete de siliciumonocristalin, există puțin spațiu de manevră pentru scăderea costului plachetelor de siliciu policristalin.
Costuri de producție a plăcilor semiconductoare
Costul plachetelorsemiconductoare este mai complex: plachetele semiconductoare au cerințe mai ridicate în ceea ce privește puritatea și caracteristicile electrice decât plachetele deenergie nouă, astfel încât sunt necesare mai multe etape depurificare și de aprovizionare cu materii prime în procesul de fabricație, ceea ce duce la o gamă maivariată de materiale de fabricație. Prin urmare, proporția costurilor cu siliciul este relativ mai mică, darproporția costurilor de producție este relativ mai mare. Între timp, în raport cucostul plachetelor de siliciu pentru energie nouă, plachetele de siliciu pentrusemiconductori din materiale directe reprezintă principala componentă acosturilor de exploatare: pentru plachetele de siliciu pentru semiconductori,costurile materiilor prime reprezintă principalul cost, reprezentând aproximativ 47% dinprincipalele costuri de exploatare. Aceasta este urmată decosturile de producție, care reprezintă aproximativ 38,6%. La fel ca și în cazul industriei producătoarede semiconductori, industria plăcilor de siliciu este o industrie cu utilizareintensivă a capitalului, cu o cerere ridicată deinvestiții în active fixe, ceea ce va genera costuri de producție mai mari din cauza deprecierii activelor fixe, cumar fi mașinile și echipamentele. În cele din urmă, există costuri directe cu forța de muncă, care reprezintă aproximativ 14,4%.
Polisiliciul este principalacomponentă a costului materiilor prime: Din costurile materiilorprime pentru fabricarea plăcuțelor de siliciu, polisiliciul este principala materieprimă, reprezentând aproximativ 30,7%. Aceasta este urmată dematerialele de ambalare, care reprezintă aproximativ 17,0%. Deoarece plachetele desemiconductori au cerințe ridicate în ceea ce privește curățenia și vidul, în special în cazul plachetelor de siliciu,care sunt foarte sensibile la oxidare, cerințele pentru ambalare sunt mult mai ridicate decât celepentru plachetele de energie nouă. Prin urmare, materialele de ambalare reprezintă oproporție mai mare din componenta de cost. Creuzetele de cuarț reprezintă aproximativ 8,7% din costul materiei prime. Creuzetulde cuarț utilizat la fabricarea plachetelor semiconductoare este, de asemenea, uncreuzet de unică folosință, dar proprietățile fizice și termice ale creuzetului sunt mult mai exigente.Lichidele de lustruire, discurile de șlefuit și plăcuțele reprezintă un total de 13,8% și sunt utilizate în principal în procesul de lustruirea plăcilor de siliciu.
Utilitățile reprezintă aproximativ 15% din costurile de producție: Costul total al utilităților reprezintă aproximativ 15% din totalul costurilor de producție, cu o pondere de aproximativ 11,4% pentruelectricitate și de aproximativ 3,4% pentru apă. În ceea ce privește sumele corespunzătoare, costul total al energiei electrice și al apei este comparabil cu costul materialelor deambalare și reprezintă aproximativ jumătate din materialul de polisiliciu, potrivit datelorfinanciare din 2018 ale Silicon Industries Group. Costurile de energie electrică suntpuțin mai mari decât cele ale creuzetului de cuarț, cu aproximativ 20%.
Bariere majore în calea producției de wafere
Obstacolele din caleaplachetelor de siliciu sunt ridicate, în special în cazul plachetelor desemiconductori, și există patru bariere principale: bariere tehnice, bariere decertificare, bariere legate de echipamente și bariere financiare.
Bariere tehnice: Specificațiile tehnice ale plachetelor de siliciu sunt relativmari, excluzând dimensiunea obișnuită, grosimea plachetelor lustruite etc., precum și deformarea, rezistivitatea, curbura etc. aplachetei. În cazul plachetelor principale de 300 mm, procesul avansat necesită ouniformitate mai mare a plachetelor, astfel încât, în comparație cu plachetele de 200 mm, planeitatea, deformarea,curbura, reziduurile metalice de suprafață și alți parametri sunt adăugați pentru a monitoriza cerințele de calitate ale plachetelor de 300 mm. În ceea ceprivește puritatea, plăcuțele cu proces avansat necesităaproximativ 9N (99,9999999999999%) - 11N (99,9999999999999%), ceea ce reprezintăprincipala barieră tehnică pentru furnizorii de plăcuțe. Plachetele de siliciu sunt produse extrem depersonalizate; puritatea este cel mai important parametru al plachetelor desiliciu și reprezintă principala barieră tehnică. În plus, plachetele de siliciu nu sunt un produsuniversal și nu pot fi reproduse. Plachetele mari de siliciu au specificații complet diferite de la o turnătoriela alta, iar aplicațiile diferite ale fiecărui produs final pot duce la specificații complet diferite pentru cerințele privind plăcuțele de siliciu. Acest lucru obligă producătoriide discuri de siliciu să proiecteze și să fabrice discuri diferite pentru diferite produse aleclienților finali, ceea ce face ca aprovizionarea cu discuri de siliciu să fie și mai dificilă.
Bariere de certificare: Producătoriide cipuri au cerințe stricte privind calitatea diferitelor materii prime și sunt foarte atenți la selectarea furnizorilor. Existăbariere ridicate la intrarea pe listele de furnizori ale producătorilorde cipuri. De obicei, producătorii de cipuri vor solicita furnizorilor de plachetede siliciu să furnizeze unele plachete pentru producția de probă, iar majoritatea acestora sunt utilizate pentruplachete de testare, mai degrabă decât pentru plachete de producție în masă. După ce trec plachetele de testare, vor produce loturimici de plachete de producție în masă pe bază de probă. După ce trece de certificarea internă,producătorul de cipuri va trimite produsele către clienții săi din aval și va obține certificarea clientului lor înainte decertificarea finală a furnizorului de plachete și, în cele din urmă, va semna un contract de achiziție. Este nevoie de mult timp pentru ca produsele uneicompanii producătoare de plăci semiconductoare să intre în lanțul de aprovizionare al producătoruluide cipuri, iar perioada minimă de certificare pentru noii furnizori este de 12-18luni. În plus, bariera de certificare de la napolitanele de testare lanapolitanele de producție în masă: în prezent, cele mai multe napolitane interne de 12inci rămân în oferta de napolitane de testare, dar procedurile de certificarepentru napolitanele de testare și napolitanele de producție în masă sunt complet diferite, iar standardele de certificarepentru napolitanele de producție în masă sunt mai stricte. Plachetele de testare trebuie să fiecertificate doar de către turnătoria însăși, deoarece nu fabrică cipuri, și trebuie să fie certificate doar la locul de producție actual. Cu toate acestea, în cazul plachetelorpentru producția de masă, acestea trebuie să fie certificate de către clientul final fără fabrică și monitorizate pe parcursul tuturor etapelorprocesului de fabricație înainte de a putea fi furnizate în volum. În general, pentru a menține o aprovizionare stabilă cusiliciu și o producție stabilă de cipuri. Odată ce un producător de wafer și un furnizor de siliciu au stabilit o relație de aprovizionare, nu schimbă cu ușurință furnizorii, iar ambele părți stabilesc mecanisme de feedback pentru a satisfacecerințele individuale, iar aderența dintre furnizorul de siliciu și client continuă să crească. Noii producători de wafere care se alăturăfurnizorilor trebuie să ofere o relație mai apropiată și wafere de o calitate mai bună decât furnizorii inițiali. Deci, în industria de wafer de siliciu,furnizorii de wafer și producătorii de wafer sunt mai lipicioși și este mai dificil pentru furnizorii mai noi să rupălipirea.
Bariere de echipamente:Echipamentul de bază pentru fabricarea plachetelor de siliciu estecuptorul monocristalin, care poate fi descris ca fiind "mașina de litografie" în cazul plachetelor desiliciu. Principalii producători internaționali de plachete de siliciu își fabrică propriile cuptoare monocristaline. De exemplu,cuptoarele monocristaline ale Shin-Etsu și SUMCO sunt proiectate și fabricate în mod independent de cătrecompanie sau prin intermediul holdingului său și nu pot fi achiziționate de alți producători de wafer. Alți mari producători de wafer au proprii furnizori independenți de cuptoare monocristaline și semnează acorduri stricte de confidențialitate, ceea ce face ca producătoriiexterni de wafer să nu poată achiziționa sau să poată achiziționa doar cuptoare monocristaline comune, în timp cepentru cuptoarele monocristaline cu specificații înalte nu pot fi furnizate. Deci, barieraechipamentului este, de asemenea, motivul pentru care producătoriiinterni nu pot intra în rândul furnizorilor principali de plăci desiliciu la nivel mondial.
Bariere financiare: Procesele defabricare a plachetelor semiconductoare sunt complexe și necesită achiziționarea de echipamente de producție avansate și costisitoare, care trebuie, de asemenea, să fiemodificate și depanate în mod constant în funcție de diferitele nevoi ale clienților. Din cauza costurilor fixe ridicate, cum ar fiamortizarea echipamentelor, modificările cererii din aval au un impact mai mare asuprautilizării capacității de producție a întreprinderilor producătoarede plăci de siliciu și, prin urmare, asupra profiturilor întreprinderilor producătoarede plăci de siliciu. În special, companiile nou intrate în industria plăcilorau fost în pierdere aproape până când au ajuns la livrări la scară largă,necesitând bariere mari de capital. În plus, deoarece fabricile au un ciclulung de certificare a plachetelor de siliciu, aceastăperioadă necesită investiții continue din partea producătorilorde plachete de siliciu, ceea ce necesită, de asemenea, o sumă mare de capital.